در ابتدا به چند ویژگی برجسته و مهمترین مزایای EPDM در برابر سایر رابرهای سنتزی پر مصرفی چون SBR, PBR, … نگاهی کنیم:
- فرایند پذیری بسیار عالی
- پایداری جوی
- پایداری حرارتی
- عایق بسیار عالی در برابر الکتریسیته
- مقاومت شیمیایی بینظیر
- و خواص مکانیکی خوب در دماهای منفی
همین مشخصات در کنار قیمت رقابتی باعث نفوذ EPDM به طیف گسترده ای از کاربری های مختلف شامل قطعات خودرو، عمران و ساختمان و صنعت برق و الکترونیک شده است و این رابر را به سومین رابر پر مصرف دنیا تبدیل کرده است. EPDM در بسیاری از کالاهای روزمره ای که در پیرامون ما دیده می شوند به شکل لوله، نوار، واشر و اورینگ، روکش کابل و … وجود دارد. در این بخش می خواهیم در خصوص مهمترین پارامتر هایی که در حین انتخاب گرید مناسب EPDM برای هر کاربری بایستی مدنظر قرار گیرد، صحبت کنیم.
فرض کنید بر اساس الزامات کاربری مد نظر EPDM گزینه ای معقول و مناسب است. این الزامات موارد فنی مختلفی را چون خواص مکانیکی ( مانند استحکام، پارگی، ضربه و …)، خواص شیمیایی ( مقاومت در برابر حلال، سیال و …)، خواص الکتریکی و حرارتی و … در بر می گیرند. اما می خواهیم ببینیم پارامترهای مهندسی که در انتخاب گرید EPDM مناسب اثر گذارند، چه مواردی هستند.
می توان گفت موارد زیر تعیین کننده عملکرد و کارایی یک قطعه بر پایه EPDM هستند:
- گرید EPDM پایه
- دیگر اجزای رابری موجود ( برای مثال قطعه مورد نظر ما تنها متشکل از EPDM است یا ترکیبی از EPDM با دیگر رابرها؟)
- وجود تقویت کننده های آلی و معدنی ( مانند Carbon black و …)
- وجود انواع روغن ها
- سیستم پخت قطعه
- فرایند تولید و شکل دهی قطعه
تمامی موارد بالا بر عملکرد و کیفیت قطعه نهایی اثر گذارند. اما به صورت ویژه در مورد گرید EPDM انتخاب شده که محل بحث ما است، توجه به موارد زیر حیاتی است.
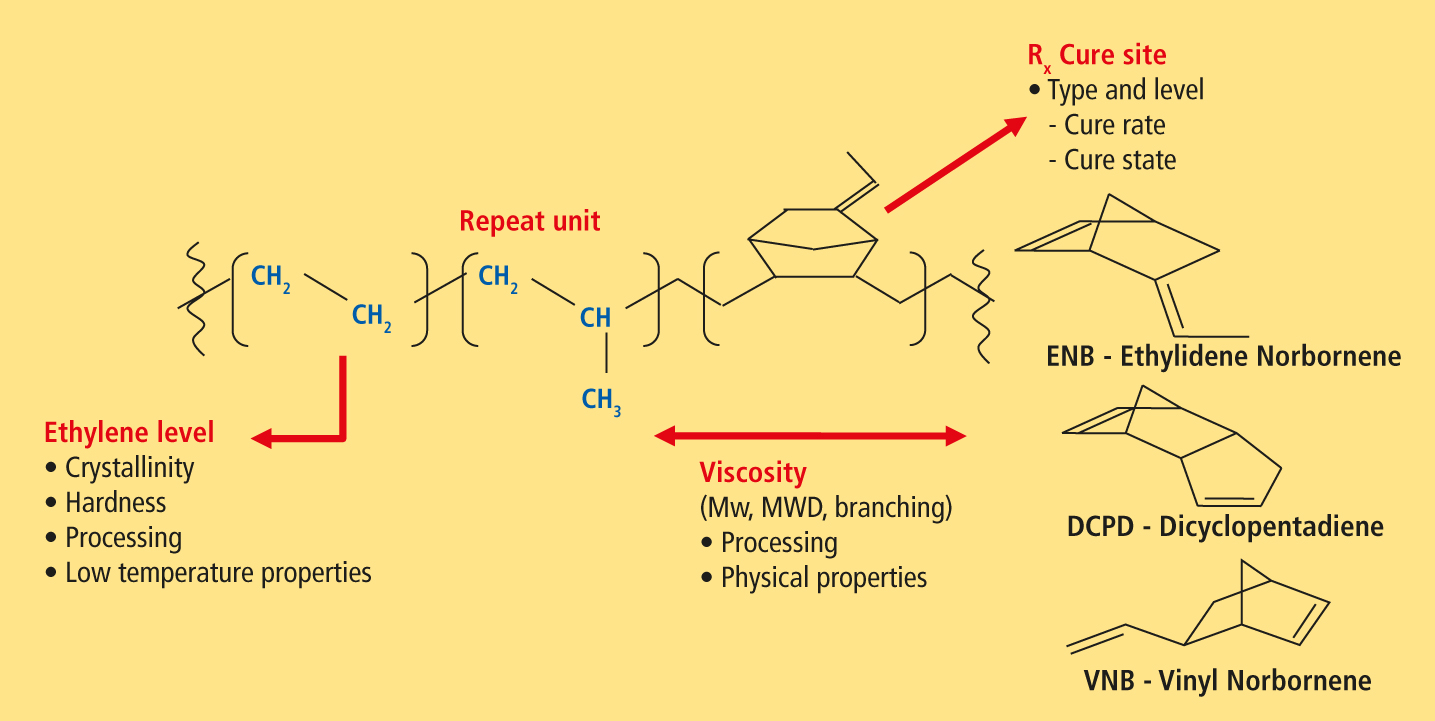
خواص و رفتار عملکردی یک گرید EPDM تحت تاثیر عوامل زیر است:
- جرم مولکولی
- توزیع جرم مولکولی
- درصد اتیلن موجود در ساختار
- درصد منومر Diene عامل پخت ( برای مثال ENB)
- وجود روغن در ساختار
- تکنولوژی تولید و کاتالیست استفاده شده
به صورت کلی با افزایش جرم مولکولی خواص مکانیکی EPDM تقویت می شود. برای مثال استحکام مکانیکی رابطه مستقیم با جرم مولکولی دارد. جرم مولکولی را می توان به کمک اعداد مربوط به ویسکوزیته مونی گرید ارزیابی کرد و این دو پارامتر رابطه مستقیم با یکدیگر دارند. بایستی در نظر داشت جرم مولکولی تعیین کننده وضعیت شکل دهی گرید مورد نظر نیز می باشد. همچنین توزیع جرم مولکولی گرید مورد نظر نیز مهم است و به صورت کلی گریدهای با توزیع جرم مولکولی پهن فرایند پذیری و شکل پذیری بهتری دارند و گریدهای با جرم مولکولی باریک خواص مکانیکی بهتری دارند. درصد اتیلن نیز تعیین کننده خواص مکانیکی همچون استحکام است. در شرایط ثابت با افزایش درصد اتیلن سختی و استحکام گرید مورد نظر افزایش می یابد. اما در مورد سرعت پخت بایستی به سراغ درصد Diene Monomer رفت و در یک گرید با افزایش درصد این بخش، سرعت پخت نیز افزایش می یابد.
در پایان بایستی در نظر داشت از آنجاییکه EPDM در تولید قطعات مهندسی نیز به کار گرفته می شود، ارزیابی پارامتر مانایی فشاری یا همان Compression Set نیز مهم است و با افزایش جرم مولکولی و همچنین Diene Monomer، مانایی فشاری کاهش می یابد.