چالش همه گیری بیماری کرونا و متعاقب آن رکود حاصل در تجارت جهانی و سایر عوامل دست به دست هم دادند تا تلاطم و نوسان عمیقی در قیمت مواد اولیه پلیمری بوجود آید و برخی مواد، مرزهای روانی قیمتی را درنوردند که در تخیل هیچ صنعتگری نمی گنجید. این نوسان و افزایش به عمق رکود دامن زد و کمک کرد تا کاربرد برخی الاستومرها به فراموشی سپرده شود.
واحد تحقیق و توسعه شرکت(Imperial Waterproofing Industries Pvt Ltd) IWIPL برای برون رفت از این بحران به ارائه دو گونه جدید از آلیاژ NBR/PVC، با نام تجاری Rubaloy پرداخته است.
Rubaloy-7060RP :
آلیاژ 7060RP که با روغن نیز گسترانده شده، راهکار نوینی را پیش پای آمیزه سازان این آلیاژ در جهت رفع مشکلات نهاده است. این الاستومر ، دارای آنتی اکسیدانت های غیر لکه زا، مقاومت عالی در برابر سایش، ازن، روغن و شرایط جوی می باشد که این خواص را مدیون انتخاب گونه خاصی از PVC برای آلیاژسازی می باشد. در نتیجه این آلیاژ ویژه فرایند پذیری سهل الوصولی در ماشین آلات رایج دارد. از جذب فیلر و روغن بسیار خوبی سود می برد که منتهی به زمان چرخه آمیزه سازی کوتاه و همراه با هزینه انرژی و نیروی کار بسیار کم می شود.
Polymer Ratio |
70:30 |
Specific Gravity |
1.06 ± 0.02 |
Raw Polymer Hardness, Shore A |
60 ± 5 |
Mooney Viscosity (ML 1 + 4 @ 100° C) |
60 ± 5 |
Extraction Percentage, Min. |
9 |
Stabilizer |
Non-Staining |
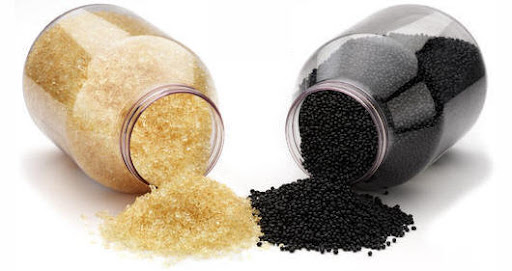
این آلیاژ با DOP, DOA, DOS, DBP, TCR, CPO و سایر پلاستی سایزرهای آروماتیک سازگار است. همچنین سختی پایین تر این آلیاژ در مقایسه با سایر آلیاژهای رایج، آن را به انتخاب مناسبی برای آمیزه های نرم تبدیل می کند.
Rubaloy 7060RP با نسبت 70:30 از NBR:PVC دارای دانسیته ای برابر با 1.06 g/cc است. سختی این آلیاژ حدود 60 Shore A است و ویسکوزیته مونی آن در شرایط (ML 1 + 4 @ 100° C) برابر با 60 است. از جمله کاربردهای اصلی این گونه می توان به موارد زیر اشاره کرد:
لایه های داخلی و خارجی شلنگ های سوخت ، تسمه نقاله ، شلنگ های LPG,CNG ، قطعات خودرویی ، گسکت، کاسه نمد، زیره کفش آنتی استاتیک و مقاوم در برابر روغن، شیت های الاستومری، قطعات اکسترودری، غلطک های چاپ ، اسفنج/ فوم های الاستومری جهت عایق کاری و نوارهای خودرویی
Rubaloy-NBP3050 :
Rubaloy-NBP3050 گونه ای است که می تواند به عنوان جایگزینی برای NBR خالص به کار رود و یا به عنوان یک گونه NBR-PVC جدید که انعطاف پذیری بالاتر، مقاومت روغن/سوخت و مانایی فشاری بهتری در مقایسه با سایر گونه ای متدوال NBR/PVC دارد ، مورد استفاده واقع شود. در این آمیزه نسبت ترکیب منحصر به فردی از NBR و PVC منظور شده و در کنار آن ، از آنتی اکسیدانت غیر لکه زا بدون رنگ نیز بهره گرفته شده است. درصد پایین پی وی سی ، به Rubaloy-NBP3050 کمک می کند تا خواصی مشابه NBR نشان دهد و در عین حال مزایای ترکیبات NBR-PVC، به ویژه مقاومت در برابر ازن، پرداخت سطح و قابلیت پردازش برتر را حفظ کند.
Polymer Ratio |
85:15 |
Specific Gravity |
0.99 ± 0.02 |
Raw Polymer Hardness, Shore A |
42 ± 5 |
Mooney Viscosity (ML 1 + 4 @ 100° C) |
52 ± 5 |
Extraction Percentage, Min. |
3 |
Stabilizer |
Non-Staining |
از جمله کاربردهای اصلی این آمیزه می توان به موارد زیر اشاره کرد:
کاسه نمد های مقاوم در برابر روغن/سوخت ، گسکت / ارینگ ، لایه داخلی شلنگ های سوخت ، زیره کفش ، قطعات خودرویی قالبگیری و جایگزین NBR در بسیاری از کاربردهای به ویژه جایی که مقاومت در برابر ازن نیز مطرح است.
شرکت پلیمر پیشرفته دانا در همکاری با شریک تجاری و فنی خود، IWIPL، و به منظور توسعه و گسترش کاربرد NBR/PVC در رقابت با NBR این گونه را به بازار عرضه نموده است.