حدود یک دهه است که عضو جدیدی به درب های مورد استفاده در ظروف بسته بندی اضافه شده است. اگر دقت کرده باشید درب ظروف غذاهای آماده و نیمه آماده، لبنیات، برخی از محصولات پروتئینی، سبزی و میوه های برش خورده یک نوع فیلم پلیمری است که در صنعت بسته بندی آن ها را Lid یا درب پوش می نامیم. در این بخش در ارتباط مکانیسم های چسبیدن این درب پوش ها به ظرف پایه صحبت خواهیم کرد و در مورد گروه خاصی از آن ها موسوم به درب های آسان باز شو یا Easy Open Lid صحبت خواهیم کرد.
مزیت اصلی فیلم های Lid در بسته بندی هایی که نیاز به یک ظرف دارند، امکان حفظ یکپارچگی بسته بندی است. این نکته به کمک یک درب عادی که پیچ می شود یا روی ظرف قرار می گیرد، یا در برخی حالات به کمک پیچاندن فیلم های پلیمری به دست نمی آید. در حقیقت تمامی راه حل های ذکر شده نمی توانند عملکرد بسته بندی را به منظور حفاظت از محتوای درون آن ضمانت کنند. این مورد در خصوص بسته بندی مواد غذایی بسیار حائز اهمیت است. در واقع به کمک درب پوش ها می توان تمامی خواصی که ظرف بسته بندی دارد را حفظ نمود و از طرفی به کمک دوخت مناسب درب پوش به ظرف پایه، عملکرد بسته بندی نیز تضعیف نشود.
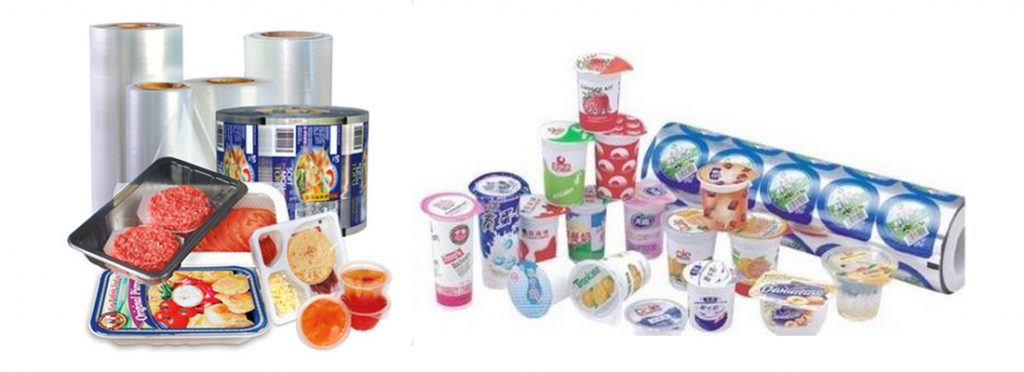
اما به منظور حفظ یکپارچگی مطرح شده در بالا این درب پوش ها بایستی بتوانند با ظرف پایه توسط عملیات حرارتی دوخت شوند و استحکام دوخت کافی ایجاد کنند. در بخش قبلی در ارتباط با پلیمرهای مورد استفاده در لایه دوخت صحبت کردیم.
ظروف مورد استفاده در بسته بندی ها معمولا به کمک پلیمرهایی چون PE, PP, HIPS, PET, PVC, PBT, … تولید می شوند. این ظروف حتی می توانند به صورت چند لایه و متشکل از پلیمرهای مختلفی به منظور دست یابی به خواص ویژه در بسته بندی ها، مانند نفوذ ناپذیری در برابر گازهایی چون اکسیژن، باشند و به منظور افزایش زمان ماندگاری محصولات مورد استفاده قرار گیرند. بر اساس الزامات بسته بندی و خواص مورد نیاز، جنس درب پوش نیز مشخص می شود. این فیلم ها نیز می توانند به صورت تک لایه یا چند لایه و حاوی پلیمرهایی چون PE, PP, PET, PA, EVOH باشند یا در مواردی حتی از انواع ورق های فلزی تشکیل می شوند. پس از مشخص شدن جنس درب پوش بایستی میزان استحکام دوخت مورد نیاز بر اساس کاربری تعیین شود.

در بسیاری از مواد غذایی نیمه آماده و آماده به درب پوش هایی نیاز است که با نیروی کمی باز شوند. این درب پوش ها که در صنعت بسته بندی به درب پوش های آسان باز شو یا Easy Open معروفند، از نظر میزان استحکام چسبندگی به ظرف پایه در محدوده ای قرار می گیرند که با نیروی حداقلی باز شوند که همزمان یکپارچگی بسته بندی حفظ شود و همچنین کاربر به راحتی بتواند درب بسته بندی را باز کند. این کار دانش وسیعی نیاز دارد و پارامتر کلیدی است. به همین منظور شرکت های پلیمری معظم و بزرگ که در حوزه بسته بندی فعال هستند، پلیمر یا رزین هایی را طراحی کرده اند که با قرار گیری آن ها در درب پوش، چسبندگی به ظرف پایه تنظیم می شود. در هر مورد بایستی بر اساس جنس ظرف و درب پوش انتخاب مهندسی صورت گیرد و مقدار استفاده تنظیم شود. علاوه بر زیبایی ظاهری و حفظ کارایی بسته بندی، درپوش های Easy Open دوستدار محیط زیست نیز هستند و منجر به صرفه جویی مصرف پلاستیک ها نسبت به روش های دیگر، از جمله پیچاندن ظرف در فیلم پلاستیکی می شوند.