موفق شدیم در آخرین بخش که لینک آن در ادامه قرار داده شده است، در ارتباط با خانواده های مختلف افزودنی های استابلایزر مورد استفاده در افزایش پایداری حرارتی PVC، صحبت کنیم. با توجه به مقالات قبلی، ما می توانیم نوع مناسب پایدارکننده حرارتی یا همان استابلایزر را انتخاب کنیم. باید در نظر داشته باشیم در هر خانواده چندین گرید تجاری توسط شرکت های مختلف عرضه می شوند و مهندسین طراح فرمولاسیون باید بتوانند در مرحله اول گرید مناسب را انتخاب و سپس غلظت بهینه ای از آن را جهت استفاده در کامپاند محصول مورد نظرشان قرار دهند. در این بخش و قسمت بعدی آن در خصوص روش های ارزیابی کارایی پایداری حرارتی استابلایزرها بحث خواهیم کرد.
پایدارکننده های حرارتی ( استابلایزر) PVC، خانواده ای وسیع و متنوع – بخش دوم
تا کنون دو روش مهم جهت کمی سازی توان استابلایزرها در افزایش مقاومت حرارتی PVC توسعه داده شده است. روش اول به تست دینامیک و روش دوم استاتیک تست نام دارد. هر روش را با جزئیات بیشتری بررسی خواهیم کرد، اما در همین ابتدا لازم است بدانیم هیچکدام از این تست ها برتری نسبت به دیگری نداشته و تنها باید دقت کرد چنانچه تنها نمونه مورد نظر ما تحت دما قرار دارد، از تست استاتیک و چنانچه علاوه بر دما، نمونه در معرض تنش های مکانیکی – حرارتی نیز قرار دارد، از تست دینامیک استفاده شود. این بخش را با معرفی تست استاتیک همراه خواهیم بود.
در آزمون ارزیابی پایداری حرارتی استاتیک نمونه تولید شده با استفاده از کامپاندی که کاملا منطبق بر فرمولاسیون نهایی قطعه مورد نظر است و حاوی غلظت کافی از استابلایزر است، در معرض دمای ثابت قرار می گیرد و تغییر یکی از دو شاخص زیر مورد ارزیابی قرار می گیرد:
- تغییر رنگ نمونه ( تست آون)
- اندازه گیری زمان آزاد شدن هیدروکلریک اسید
نمونه ای که مورد آزمون قرار می گیرد، می تواند به کمک هر یک از روش هایی که در مقاله بازدهی فرمول یک محصول پایه PVC را چگونه ارزیابی کنیم؟ معرفی شدند، تولید شود. اما باید در نظر داشت همه نمونه ها تحت شرایط ثابتی تهیه شوند.
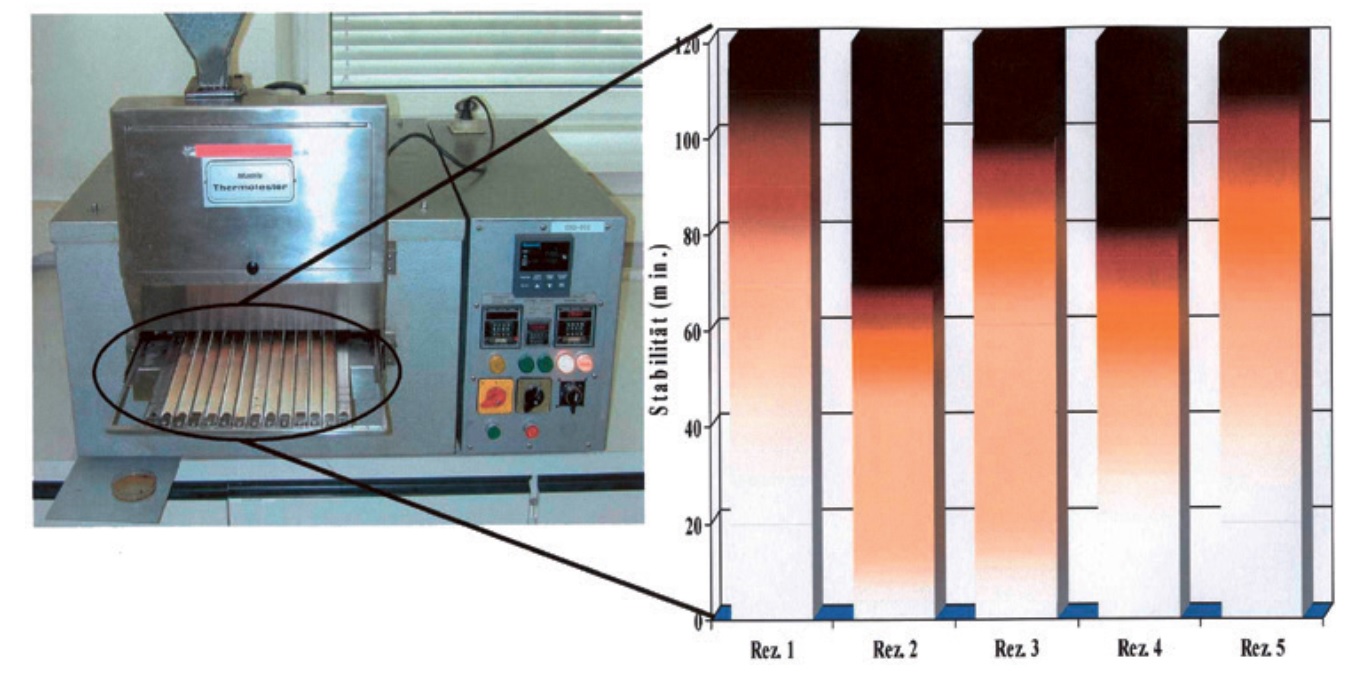
در روش آون یا همان بررسی تغییر رنگ نمونه، باریکه هایی از فیلم های تهیه شده از نمونه مورد نظر در دمای ثابتی ( معمولا دمای 170-200 °C) درون آون قرار می گیرند و در زمان های مختلف (برای مثال هر ده دقیقه یک بار) نمونه برداری صورت می گیرد و تغییر رنگ نمونه ها نسبت به یکدیگر ارزیابی می شود. با توجه به اینکه امکان اندازه گیری تغییر رنگ به صورت کمی نیز مهیا ( برای اطلاعات بیشتر مراجعه کنید به روش های ارزیابی کیفیت و ثبات رنگ قطعات تولید شده با PVC) است، بنابراین این روش اطلاعات کاملا کمی را حاصل می کند. این روش بیشتر در کاربری های PVC نرم مورد استفاده قرار می گیرد.
اما در روش تعیین زمان آزاد شدن هیدروکلریک اسید، به تجهیزات پیشرفته تری نیاز داریم. در این روش نمونه حرارت داده می شود و جریان هوا، نیتروژن یا آرگون در محفظه ای که نمونه در آن قرار دارد، وجود دارد. گاز خروجی از محفظه نمونه وارد آب بدون یون می شود و PH این آب مرتبا اندازه گیری می شود. به محض شروع تولید گاز هیدروکلریک اسید PH آب کاهش می یابد. مدت زمانی که طول می کشد اولین کاهش در PH آب رویت شود، همان زمان پایداری استاتیک نمونه PVC مورد آزمون است. این روش بنام دی هیدروکلرینیشن (Dehydrochlorination) نیز شناخته می شود و معمولا برای فرمولاسیون های PVC سخت و کدر، مانند لوله و پروفیل درب و پنجره مورد استفاده قرار می گیرد.