ECO رابری با خواص فوق العاده تر نسبت به NBR
(Epichlorohydrin Rubber (ECO، اپی کلروهیدرین، رابری سنتزی و حاصل از همو پلیمریزاسیون یا کوپلیمریزاسیون کلرومتیل اکسیران (Chloromethyloxirane) یا همان اپی کلروهیدرین (Epichlorohydrin)، و اکسیران (Oxirane) یا همان اتیلن اکساید (Ethylene Oxide) است. این رابر شدیدا مشابه NBR است و در حقیقت می توان گفت نسخه ی بهبود داده شده NBR است. برای مثال مقاومت حرارتی، پایداری در برابر ازون و انعطافپذیری بیشتری در دماهای پایین در مقایسه با NBR دارد. مقاومت در برابر ازون ECO بدون نیاز به اضافه شدن افزودنی های آنتی ازون به اندازه کامپاندهای رابری است که حاوی افزودنی های آنتی ازون هستند. از جمله دیگر ویژگی های ECO می توان به نفوذپذیری ناچیز در برابر گازهای مختلف، (برای مثال نفوذپذیری Epichlorohydrin Rubbe در برابر هوا از رابر بیوتیل که پرچم دار رابرهای نفوذناپذیر در برابر هوا است، نیز کمتر است)، پایداری بینظیر در برابر شرایط جوی، مانایی فشاری کم، مقاومت عالی در برابر روغن ها اشاره کرد و همچنین در برابر هیدروژن پروکساید و حلال های آلکالی نیز پایدار است. ساختار این رابر فوق العاده در تصویر زیر دیده می شود:
شاید مهمترین ایراد وارد بر اپی کلروهیدرین را بتوان در مقاوم کم آن در برابر حلال های قطبی چون الکل، آمین، استر، کتون، روغن های هیدرولیک و اسیدها دید و همچنین باید گفت مقاومت در برابر سایش این رابر کم است. بیشترین کاربرد اپی کلروهیدرین در صنایع خودروسازی و برای تولید طیف گسترده ای از واشرها، شلنگ ها، اورینگ، گسکت و تسمه ها است. همچنین Epichlorohydrin Rubbe در فرمولاسیون برخی از چسب ها نیز به کار می رود. ECO مقاومت بسیار خوبی در برابر سوخت های مختلف دارد، برای مثال مقاومت ECO در مقابل سوخت نوع C برابر با یک NBR حاوی ۵۰ درصد منومر آکریلونیتریل است.
مقاومت حرارتی خوب این رابر باعث استفاده گسترده از آن در تولید داکت و کانال های هوا و اگزوز در خودرو شده است. همچنین به دلیل مقاومت خوب ECO در برابر سوخت هایی چون بنزین و گازوئیل و همچنین قیمت به صرفه آن، در تولید شلنگ های سوخت خودرویی مورد استفاده قرار می گیرد. برای مثال مطابق تصاویر زیر ECO در تولید کانال های هوا و همچنین لایه هایی از اپی کلروهیدرین در شلنگ های چندلایه سوخت به کار می رود.
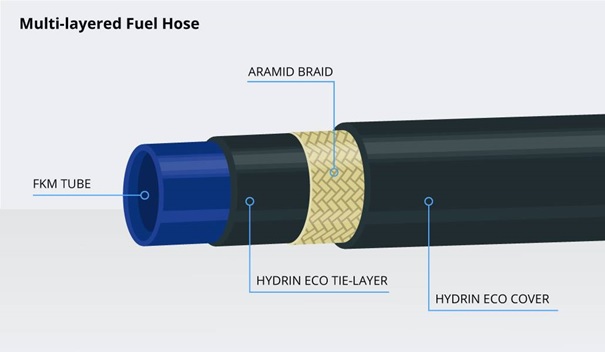
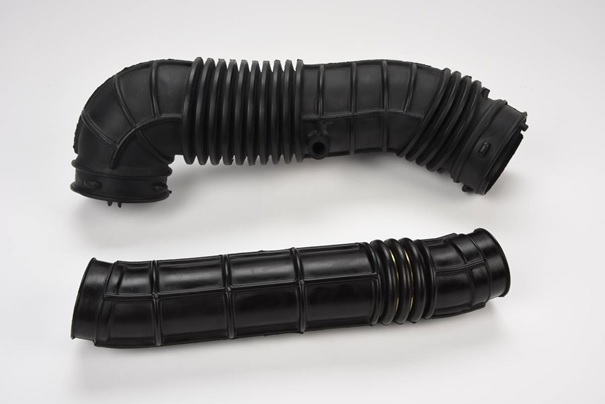
باید اضافه کرد که ضریب بالای اتلاف الکتریسیته ECO این رابر را به انتخاب اول مهندسی مواد برای روکش دهی غلتک های پرینترها کرده است.
مهمترین کمپانی های صاحب نام در تولید اپی کلروهیدرین کمپانی های زئون (Zeon) و اساکا سودا (Osaka Soda) هستند. همانگونه که در ابتدا اشاره شد گریدهای مختلف ECO را می توان در سه گروه مهم ECO-H، به عنوان همو پلیمرها، ECO-C، به عنوان کوپلیمرها و بالاخره ECO-T به عنوان تر پلیمرها قرار داد. هر کدام از گونه های مختلف ECO خواص ویژه و خاصی دارند و به صورت تنها یا آلیاژ شده با سایر گریدها استفاده می شوند. انتخاب گرید مناسب بایستی بر اساس الزامات کاربری نهایی انجام پذیرد. برای مثال ECO های هموپلیمر مانایی فشاری بهتر و در مقابل ECO های کوپلیمر ازدیاد طول در نقطه پارگی بیشتری دارند. همچنین می توان ECO را به صورت آلیاژ شده با سایر رابرها به منظور ارتقای خواص حرارتی رابر مورد نظر کامپاند و قطعات مورد نظر را تولید کرد.