افزودنی های نایلون گلخانه ای برای کنترل کشت
بدون شک نایلون گلخانه ای یکی از مهندسی ترین پوشش هایی است که با استفاده از پلی الفین ها تولید می شود. پلیمرهای مورد استفاده در فرمولاسیون این محصول انواع LLDPE, LDPE, EVA هستند. انتخاب صحیح نوع پلیمر می تواند پوشش را در برابر آسیب های مکانیکی (مانند خزش در زمان کاربری)، بارش برف، تگرگ و باران محافظت کند. همچنین انتخاب صحیح فرمول فیلم، تعیین کننده عبورپذیری پوشش در برابر نور خورشید، کنترل دما و رطوبت درون گلخانه است. به دلایل ذکر شده نایلون گلخانه ای یک محصول کاملا مهندسی است. باید توجه داشت که برخی از خواص مورد نظر با انتخاب صحیح پلیمرهای پایه بدست می آید و بخشی دیگر را بایستی به کمک افزودنی ها در نایلون گلخانه ای ایجاد نمود.
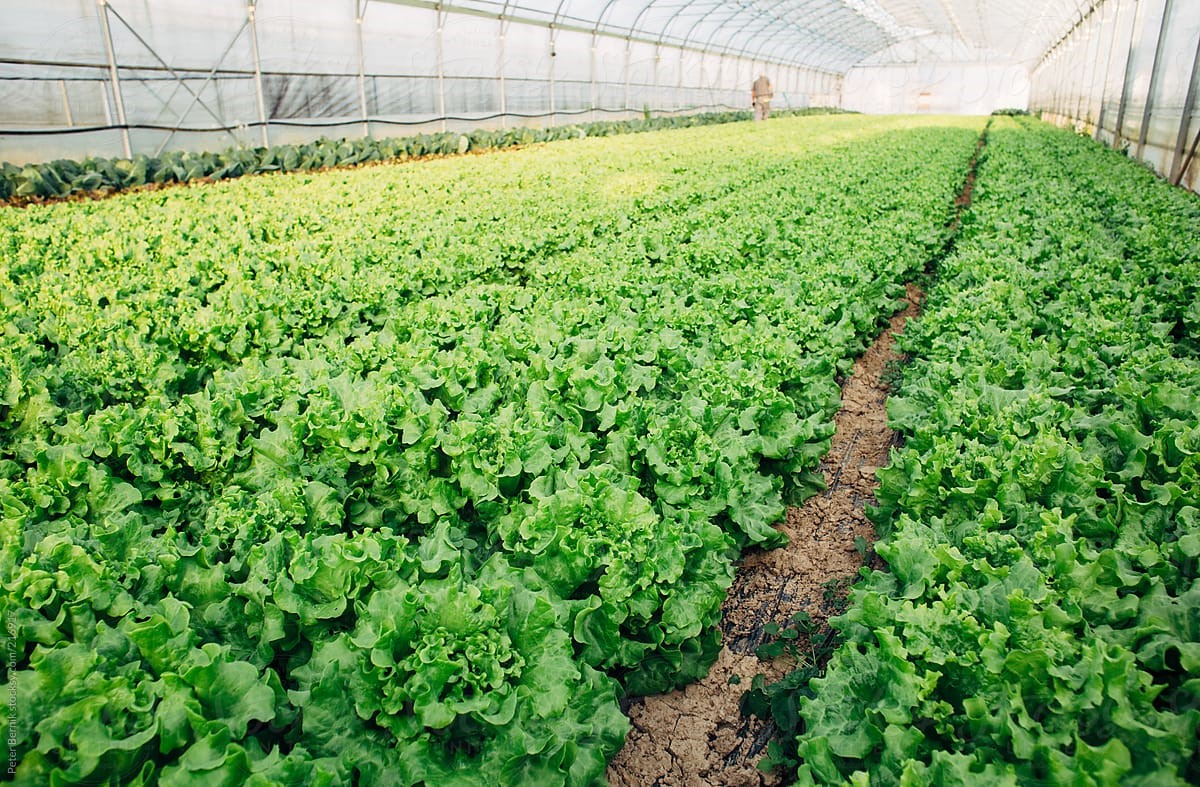
افزودنی های نایلون گلخانه ای
پس از انتخاب صحیح پلیمرهای پایه نایلون گلخانه ای، مهمترین افزودنی هایی که در تولید این محصول به کار می روند را می توان در گروه های زیر قرار داد:
- بهبود دهنده طول عمر
برای افزایش طول عمر نایلون گلخانه ای، بایستی مستربچ های پایدارکننده در برابر اشعه فرابنفش استفاده شود. برای مطالعه بیشتر در باره این افزودنی ها به مقالات زیر مراجعه کنید:
پایدارسازی فیلم های گلخانه در برابر نور خورشید
مقاوم سازی پلاستیک ها در برابر نور خورشید
- بهبود دهنده خواص نوری
نور مورد نیاز برای رشد گیاهان، نور PAR (Photo synthetically Active Radiation) است. این نور در محدوده طول موج 400-700 nm قرار میگیرد و برای رشد اندام های گیاه لازم است. نایلون گلخانه بایستی حداکثر عبوردهی نور را در این محدوده داشته باشد و مابقی طول موج ها را فیلتر کند. در بخش های بعدی در مورد این افزودنی ها بیشتر صحبت خواهد شد.
- تنظیم خواص سطحی
به دلیل طبیعت غیر قطبی پلیمرهای مورد استفاده در تولید نایلون گلخانه ای، در زمان کاربری و با بالا رفتن درصد رطوبت یا نوسانات دمایی در محیط گلخانه، قطره های آب روی سطح داخلی نایلون گلخانه تشکیل می شود. این قطرات مشکلات متعددی همچون انعکاس نور، سوختگی برگ گیاهان و ایجاد قارچ و آفت روی گیاهان ایجاد می کنند. با استفاده از افزودنی های آنتی فاگ (Anti-fogging) قطرات آب ایجاد شده روی سطح فیلم به یک لایه آب تبدیل می شود.
- بهبود فرایند تولید
برای بهبود فرایند اکستروژن نایلون گلخانه ای و باتوجه به اینکه در برخی موارد این محصول به صورت چند لایه تولید می شود، استفاده از برخی افزودنی ها می تواند راهگشا باشد. برای مثال مستربچ آنتی اکسیدانت می تواند مقاومت حرارتی را در حین فرایند تولید افزایش دهد. (برای مطالعه بیشتر رجوع کنید به PPD – AO) یا مستربچ کمک فرایند برای دستیابی به کیفیت سطح بهتر فیلم استفاده می شود. همچنین برای کاهش اصطکاک فیلم با ماشین آلات تولید مستربچ Slip agent و برای راحت تر باز شدن نایلون در حین نصب از مستربچ های آنتی بلاک استفاده می شود.
در پایان می توان گفت انتخاب صحیح پلیمرهای پایه و افزودنی های لازم، نایلون گلخانه ای را ایجاد می کند که می تواند تولید محصولات کشاورزی با کیفیت، سالم و دارای ارزش غذایی را نتیجه دهد.